汽车用折边胶(车身涂胶连接设计与规范)
通过《ET7车身结构与涂胶连接》这篇文章,我们了解到了新能源汽车的车身结构与涂胶的质量要求,涂胶工艺是汽车白车身制造过程中非常重要的环节,随着汽车制造工艺水平的提高,车身涂胶的品种、性能和工艺规范正不断的优化改进,涂胶设备也逐渐更新换代。
目前,很多汽车制造企业已采用机器人涂胶的方式,保证了涂胶质量的稳定可靠,以满足车身的结构强度、减振降噪、NVH以及防锈密封的要求。
随着近20年来汽车行业的快速发展,国内汽车用胶厂家已有上千家,在主要品种上已基本可以满足需要,但在提高产品质量和适应汽车大批量流水线生产工艺方面,尚需做进一步的优化工作,进口用胶的依赖性仍然很高,机械化程度和标准作业同国外先进水平相比还有较大差距,配套的涂胶设备也过多的依赖进口。这些都已成为国内汽车用胶面临的亟待解决的问题。
未来汽车的发展方向是节能环保和轻量化,车身用胶也必然朝着绿色、环保和节能的方向发展。考虑目前大部分车身胶粘剂均为流体膏状物,易污染环境,固体胶逐渐代替流体胶应用在车身,例如密封用胶条、隔振胶带、补强胶片、结构胶片和膨胀胶块等已在部分车企得到了应用和推广。轻型材料如铝等,在车身上的应用日益广泛,多种不同材料、材质的粘结,对汽车用胶也提出了新的挑战,未来汽车用胶需要在粘结轻型材料和复合材料上进行突破。
兼顾高性能,绿色环保,低成本方面的开发的同时,我们更多的应该关注客户的需求,对于车身涂胶连接设计规范方面,我们也应该有更深刻的了解和认识,下面,螺丝君就和小伙伴们一起了解一下新能源车辆的白车身涂胶连接设计和规范,主要从结构胶、减震胶、折边胶、密封胶4种类型的胶进行介绍。
01 结构胶定义与设计原则
1.1 结构胶定义
以环氧树脂为基材的结构胶,具有一定的结构强度,能够有效地将车身结构件粘接在一起。应用于车身结构连接区域,主要作用是与SPR、点焊等刚性连接结合,提高整体刚度、也起到一定的密封与减震降噪的作用。结构胶主要是以改性的环氧树脂为基体的热固化结构胶,形成具有很高的拉剪强度和疲劳强度粘接结构(下图示意)。
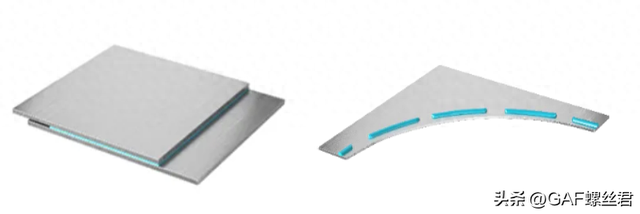
结构胶应用于受力结构件胶接场合,能承受较大动负荷、静负荷,并能长期使用的胶粘剂,代替螺栓、铆钉或焊接等形式用来接合金属、塑料、玻璃、木材等的结构部件,属于长时间经受大载荷、而性能仍可信赖的胶粘剂。除了在白车身的应用外,还应用于动力电池中,主要用于粘接电芯与电芯、电芯与泡棉、电芯和模组外壳等,使电芯与模组成为一体化,满足模组的振动、冲击和跌落等要求。
1.2 结构胶设计原则
① 结构胶适用于金属零件间隙小于1mm的结构粘接;
② 对于需要定义结构胶密封特性的,间隙应小于1mm,特殊需求、应用需要做逐一讨论。
③ 车身性能部门根据性能与设计要求,对于关键工位可以按照15mm宽度进行设计,搭接宽度应满足15mm-20mm。
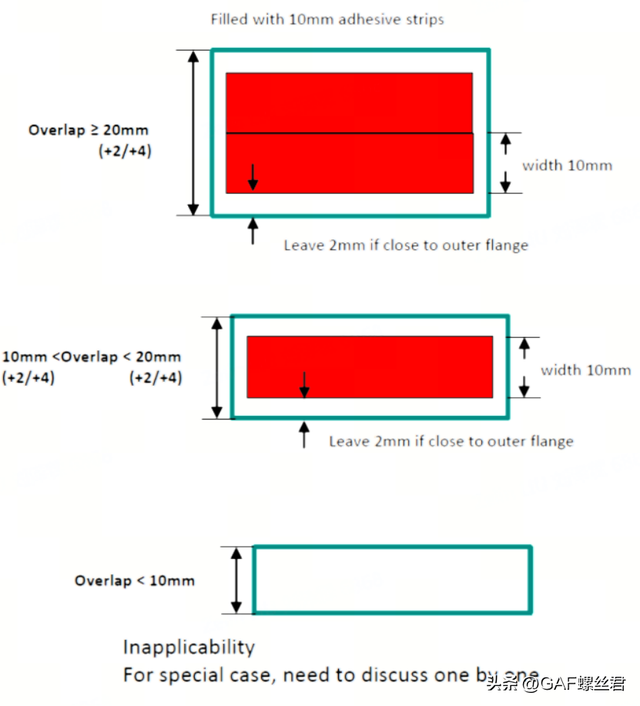
内外翻边预留至少2mm,如搭接区域有防腐要求,则要求必须100%涂胶覆盖。
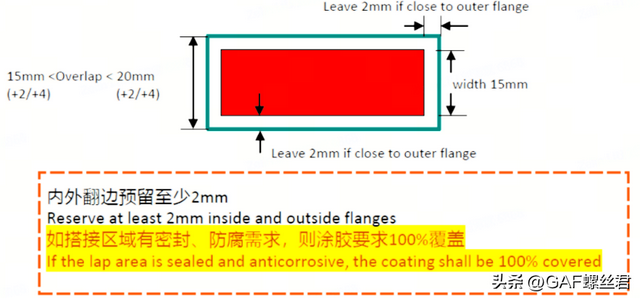
具体的设计要求如下(参考下图):
a:面板间隙
b:层压后的宽度
d:胶粘剂直径
结构胶作为密封检查项目的位置(以YCYS清单为准):
① a≤1mm(含公差),d 推荐为:(3-6)mm(如仅密封要求,b≥5mm,允许溢胶,如有连接要求,b≥10mm)
② 1<a≤ 2mm(含公差),b≥5mm,d推荐≥6mm,允许溢胶;
PVC(聚氯乙烯)作为密封,结构胶作为辅助:
① 如果只有辅助密封要求,则质量没有特别要求,可在R角连续涂胶。
② 如有连接强度要求,b≥10mm。
如果不适用上述场景,那就具体问题再进行讨论和分析。
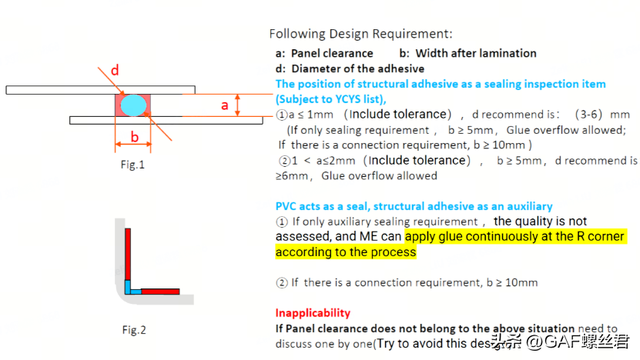
设计上要求,压开后的胶条和孔边缘距离一般在5mm左右,R角处的结构胶,如数模不设计,工程上可以按照工艺R角处连续涂胶。
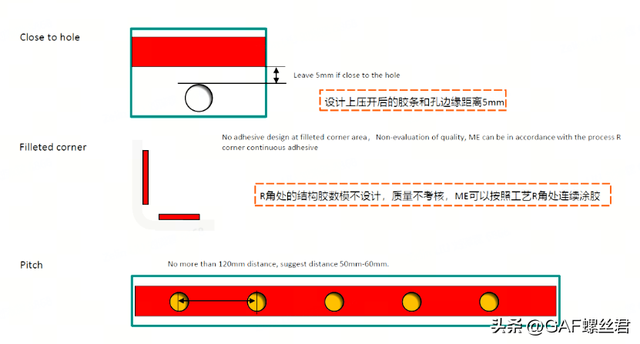
02 折边胶定义与设计原则
2.1 折边胶定义
以环氧树脂为基材的加热固化后的折边胶,具有良好的抗流性性能,受热时无腐蚀气体放出、抗腐蚀性好,不含溶剂和PVC,与油面钢板和镀锌层有良好的粘合力。应用于车门、发动机盖等的包边,采用粘接方法无应力集中现象,抗冲击效果好。与点焊比较,可减少车身上的焊点,使工艺更加美观,抗疲劳强度优于点焊。增加包边和连接钣金之间的连接力,实现防水、防尘、防锈并提高整体刚性。
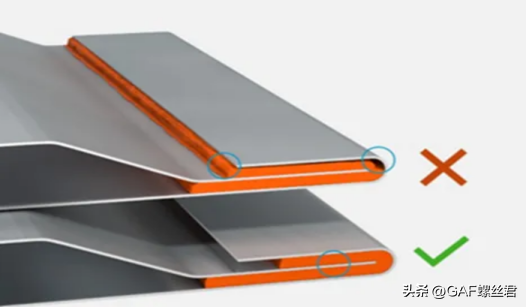
具有以下工艺特点:
1、根据不同的车型、不同部位、不同要求进行折边胶的选择;
2、涂胶部位和数量要正确;
3、冬季用胶时要选择粘度较低的产品,易于施工;
4、转角部位不要打胶,部分包边有缺口,容易挤出。
随着胶品种和性能的发展,目前应用已经不局限于四门两盖,开始在车身内部如顶盖梁等部位与点焊一起应用,增加空腔结构强度,减少局部应力,提高结构韧性,降低腐蚀。
2.2 折边胶设计原则
2.2.1 封边粘接距离需要遵循以下原则:
适用于外板情况:
a = 6mm ~ 8mm,
b = 2mm,
L = 12mm,
D = 3mm。
适用于mini玻璃球内胶 D=0.15~0.25mm
(具体见如下示意图)
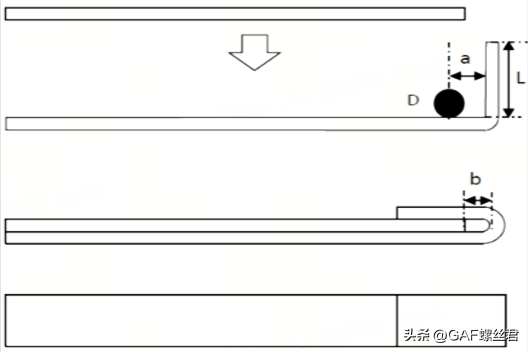
2.2.2 折边胶厚度范围:
胶粘剂厚度范围—前盖:
1、胶粘剂内添加的玻璃微珠粒径为0.15mm~0.25mm,设计间隙=0.2mm;
2、3D数据应设计为无厚度的片体(胶宽需要和内外钣搭接面宽度保待一致,如果钣金搭接面宽度不足,也允许某些位置设计宽度<10mm);
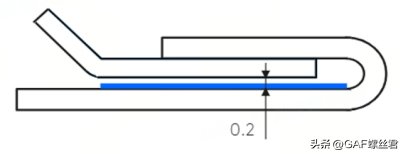
胶粘剂厚度范围——包含侧门、厂内金属尾盖、翼子板、后轮罩等:
1、胶粘剂内添加的玻璃微珠粒径为0.15mm~0.25mm,设计间隙=0.15mm;
2、宽度设计要求参考前盖。
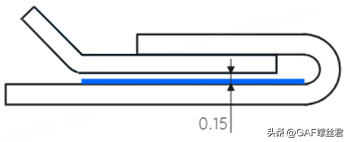
2.2.3 不同的材质的涂胶设计要求(钢&铝):
钢材料的涂胶要求:
① 全包结构:D面需保证胶水涂胶面>0mm
② 半包结构:包边弯折处有溢胶
③ 开放性包边结构:C面有溢胶,无100%填充要求
④ 水滴包边结构:D面需保证胶水涂胶面>0mm
结构参考下图
铝材料的涂胶要求:
① 铝车门包边区域为湿区,无需考核密封性
② 需要足够的粘接宽度来保证连接强度即可(具体数据依据强度验证得出)
③ 允许在特定位置进行断胶(如工艺不好实现位置)
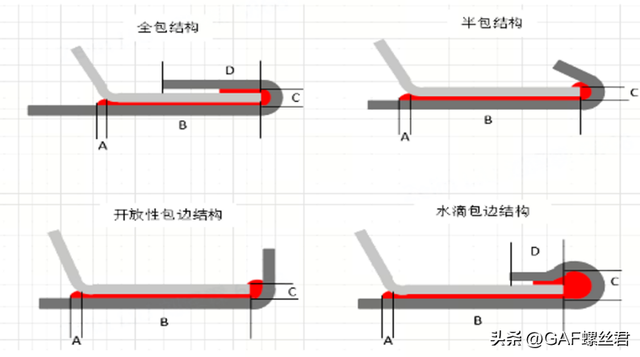
2.2.4 特殊区域要求(如侧门)
为防止折边胶过度溢出,需保持漏液孔距离折边边缘为≥17rmm(参考下图示意);
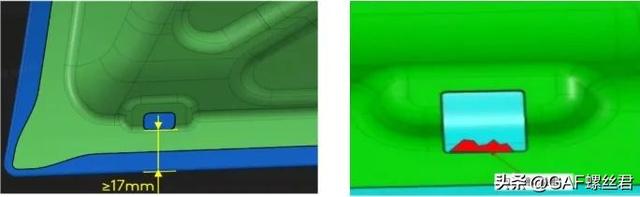
03 减震胶定义与设计原则
3.1 减震胶定义
以橡胶为基材的减震胶,分为低膨胀和中等膨胀,减震降噪效果优异,低硬度,-40℃仍可正常使用,通常用于膨胀后填充钣金之间焊点无法连接处的间隙。应用于车门、发动机盖、后备箱盖处,主要作用是减少震动和噪音,提高稳定性。
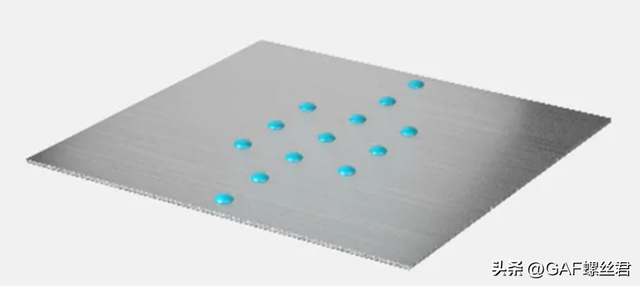
3.2 减震胶设计原则
减震胶粘接距离应遵循以下原则:
有面板槽(左图):a= 4±1mm,无面板槽(右图):a=3±1mm。
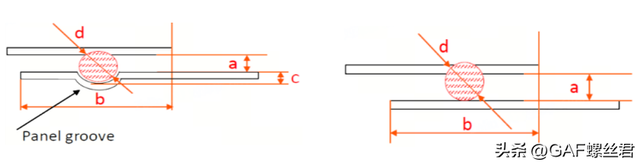
b≥15mm;
c=1.5mm;
d=6mm~7mm;
a:面板间隙;
b:嵌板重叠尺寸;
c:面板槽位深度;
d:胶粘剂直径。
04 密封胶设计原则
4.1 密封胶定义
以橡胶为基材的密封胶,在室温下具有高粘性,加热固化后变成橡胶弹性体,具有优秀的密封和防水性。应用于前围、侧围、地板等处,主要作用是密封,防止水、气、尘从地板以下或发动机舱渗透到驾驶室内,也能起到防腐蚀作用(密封效果是否OK见下图)。

密封胶以其成本低廉、无毒、无味、施工性能良好、施工工艺简单,可操作性强、密封效果优异等良好的综合性能已经成为当前车身焊缝密封的理想材料。
4.2 密封胶设计原则
缝体密封胶:
依据设计数据,要求面板间隙:≤1mm,面板重叠度:≥5mm,压后胶黏剂要求:单侧宽度≥5mm,总宽度≥15mm,厚度≥2mm。
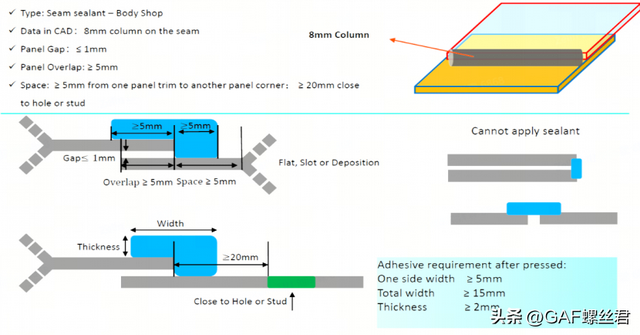
接缝处胶粘剂厚度≥2mm,单面宽度≥5mm,接缝处侧面整体宽度≥20mm,且经气密性试验密封性良好。
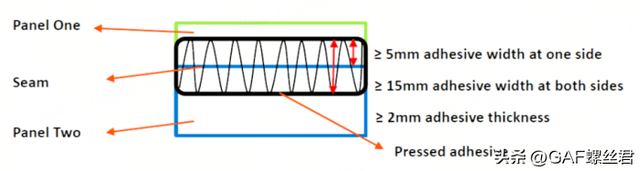
点焊密封胶(图中粉红色):
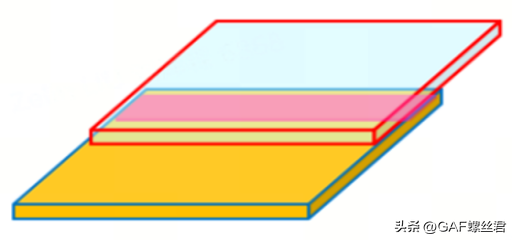
应用于车身钣金间,当车身钣金间内部有密封要求时使用。
如下图标记区域:
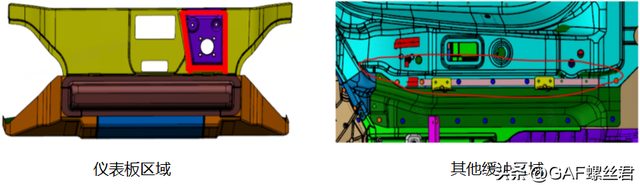
涂胶尺寸要求:
钣金间隙:≤1mm;钣金重叠度:≥12mm与预留孔距离≥5mm,如下图示意:
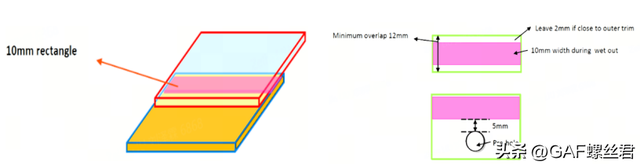
螺丝君经验与总结
以上就是我们对4种胶连接工程设计与规范的粗略讲解,车身结构轻量化之后,随着纯铝车身或者钢铝混合车身结构的设计,胶连接工艺也得到大范围的应用,对于我们的涂胶方案设计方面提出了一定的要求,从性能、成本、可靠性等方面,给出最优搭配方案。
具体的设计数据要求,需要结合车身结构及性能的要求,进行设计验证,并经过拆解、气密性检测、动态评价、车辆耐久等方式,确定具体的涂胶参数及工艺要求,上述螺丝君仅是介绍一些常规的要求,当然每个企业都会有各自的规范,欢迎小伙伴们一起探讨,后续章节我们再继续介绍一下涂胶过程控制方法与常见的质量问题。
今天的话题,就分享到这里,不当之处,欢迎批评指正;若您有任何疑问或建议,或需要进群交流的小伙伴,可关注螺丝君微信公众号:GAF螺丝君(GAF-luosijun)
- 真香!10万内插混SUV新标杆!9.98万+165km续航=蓝电E5 PLUS
- 直呼真香!10万内插混SUV新标杆!9.98万+165km续航=蓝电E5 PLUS
- 10万内插混SUV的新标杆!9.98万+165km续航=蓝电E5 PLUS
- 10万内插混SUV新标杆!9.98万+165km续航=蓝电E5 PLUS
- 蓝电E5 PLUS上新了,一口价9.98万,10万内唯一165km长续航插混SUV
- 蓝电E5 PLUS上新,一口价9.98万,10万内唯一165km长续航插混SUV
- 蓝电E5 PLUS上新,一口价只需9.98万,10万内唯一165km长续航插混SUV
- 蓝电E5 PLUS上新,一口价只要9.98万,10万内唯一165km长续航插混SUV
- 全能六边形战士,蓝电E5 PLUS 长续航先享版能够满足不同用户群体
- 全能六边形战士,蓝电E5 PLUS 长续航先享版满足不同用户群体
- 全能六边形战士,蓝电E5 PLUS 长续航先享版做到满足不同用户群体
- 全能六边形战士,蓝电E5 PLUS 长续航先享版能够满足不同的用户群体
-
真香!10万内插混SUV新标杆!9.98万+165km续航=蓝电E5 PLUS
2015.12.16 -
直呼真香!10万内插混SUV新标杆!9.98万+165km续航=蓝电E5 PLUS
2015.12.16 -
10万内插混SUV的新标杆!9.98万+165km续航=蓝电E5 PLUS
2015.12.16 -
10万内插混SUV新标杆!9.98万+165km续航=蓝电E5 PLUS
2015.12.16